Carr Machine & Tool Expands Operations
Carr's new location is a 15,000 square foot high-tech facility in which the company intends to add robotic, inspection and machine technologies.
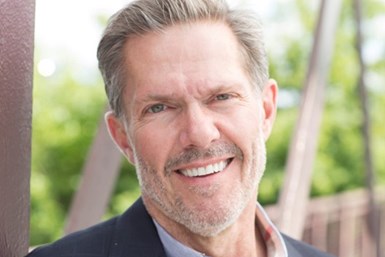
Jim Carr. Photo Credit: Carr Machine & Tool
Richard Carr opened his precision machine shop — Carr Machine & Tool — in 1972, which initially served as a manufacturer for commercial printing press parts. In 2004, the company began to focus on emerging industries when Richard’s son, Jim Carr, took full ownership as its president.
Since taking over, Carr has turned the company into a high-tech CNC shop, a process that included upgrading its ERP, obtaining AS9100D accreditation and re-focusing its interests on the aerospace, space and exploration, semiconductor, medical and defense industries. "We support clients like Virgin Galactic, Tesla and Boom Supersonic, and serve as their first-class aerospace machine shop,” Carr says.
Carr recently moved locations within the Elk Grove Village industrial park. The new location is a 15,000 square foot high-tech facility, where the company intends to grow by adding robotic, inspection and machine technologies. According to Carr, this move will result in a 300 percent expansion of operations.
“We truly ‘live’ in this industry and believe in the direction it’s going as it pertains to innovation,” Carr says. “We want to connect with clients that have the same ambition.”
RELATED CONTENT
-
Starting with the End in Mind: An Exit Strategy for Machine Shops
John Shegda and Eric Wilhelm each had different ideas about how they wanted to phase into retirement. The exit strategies for the three successful manufacturing businesses the two men operated included a mix of seeking equity groups, selling the business, or transitioning into an employee stock ownership plan. All it took was a friendly suggestion from a mutual friend to set them on a different path.
-
Where Dry Milling Makes Sense
Liquid coolant offers advantages unrelated to temperature. Forced air is the fluid of choice in this shop...but even so, conventional coolant can't be eliminated entirely.
-
Use Your Machinists to Make Dies
By systemizing die making into repeatable steps, Dies Plus, a division of Otto Engineering, is using its machinists to effectively make dies. This solution relies on a paperless color-coding system to convey the tolerances machinists need to hit in order for tool and die makers to do the final fitting.